Note. To perform the work described below, you will need a micrometer and a bore gauge.
Removing
1. Turn the crankshaft, bringing the engine to the TDC position of the end of the compression stroke of the first cylinder. In this position, the mark on the crankshaft pulley will be aligned with the pointer on the timing belt cover, and the distributor runner will turn its nose towards the location of the BB terminal of the spark plug wire of the first cylinder.
2. Remove the air cleaner.
3. Release the BB spark plug wires from the retainers on the cylinder head cover.
4. In a spiral order, moving from outside to inside, give the screws securing the cylinder head cover to the head. Remove the cover.
5. In several stages, loosen the rocker axle mounting bolts and carefully remove the axle assemblies. Lay the assemblies in the order in which they are installed on the engine.
6. To fix the valve lifters in the engine, put rubber bandages on their upper parts, then remove the pusher guides from the cylinder head.
Note. To avoid getting air into the hydraulic tappets, do not overturn or tilt them too much.
Disassembly and condition check
1. Partially disassembled assemblies of rocker arms, their axles and pushers are shown in the accompanying illustration.
Note. Axles with one mark should be installed in the front guide of the pushers, with two - in the rear. The layout of the rocker arms on the axles is clear from the illustration.
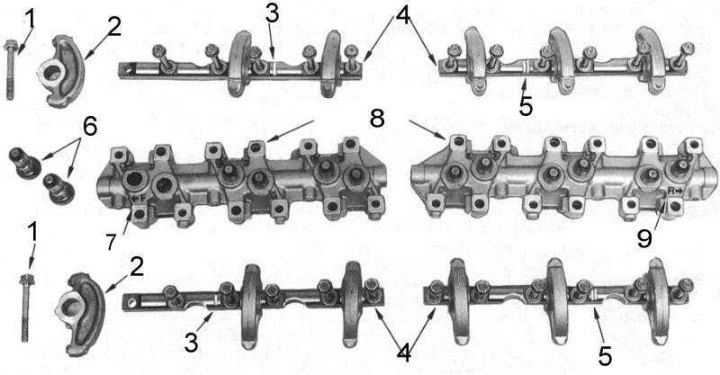
1 - bolt; 2 - rocker; 3 - one label; 4 - axes of rocker arms; 5 - two marks 6 - hydraulic pushers; 7 - front mark; 8 - pusher guides; 9 - back mark
2. Give bolts of fastening of axes of yokes. Check the condition of the axles, remove the identified burrs and burrs from them that can cause damage to the rocker seats in the process of removing the latter.
3. Remove the rocker arms from their axles by stacking them in order on the engine.
4. Check the axles for signs of wear and damage. Using a micrometer, measure the axle diameters. Compare measurement results with regulatory requirements (see tables of sizes and adjustments at the end of the guide). Replace excessively worn axles.
5. Check the condition of the landing slots (holes) rocker. If excessive wear is suspected, measure the inside diameters of the sockets. Compare the results with the data in the tables of sizes and adjustments. Replace worn rocker arms.
6. Check all tappets for signs of actuation, paying special attention to surfaces in contact with the rocker arms. Excessively worn tappets must be replaced.
Note. In the event of excessive wear of the pusher, it is necessary to carefully check the condition of the working lug of the corresponding camshaft cam.
7. Alternately squeeze the top of each of the hydraulic pushers. If the plunger is pressed deeper than 1.0 mm, the plunger must be replaced. A further check of the tappets can be made after assembly by running the engine for 10 minutes at 1,000 rpm. If during this test characteristic noises are detected, remove the components that block access to the pushers and repeat the first test. Replace all pushrods whose plungers are recessed deeper than 1.0 mm.
8. Using a micrometer, check the pusher guides for signs of excessive wear. Measure the inner diameters of the holes and the diameters of the corresponding tappets. If the clearance calculated in by subtracting from the result of the first measurement of the second clearance exceeds the specified in tables of sizes and adjustments (see end of manual), replace the relevant components.
Assembly and installation
Assembly and installation are carried out in the reverse order of dismantling.
1. Make sure that all channels and openings are open.
2. Lubricate all components with clean engine oil before assembly.
3. In the same order, put the rocker arms on the axle from which they were removed. If during the dismantling process the alignment marks were not applied and the rocker arms were mixed up, use the signs illustrated in the accompanying illustration. Please note that the pusher guides are marked and the rocker shafts with one mark must be installed in the front guide.
Note. The rocker arms are asymmetrical in design - see the accompanying illustration.
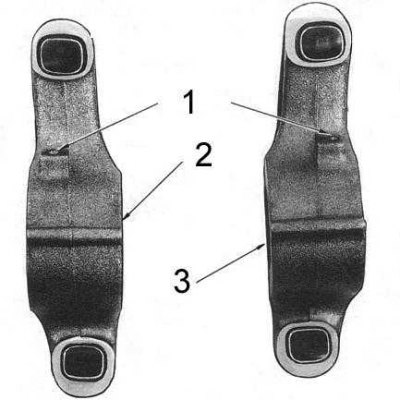
1 - oil holes
2 - cylinders 1, 2 and 3
3 - cylinders 4, 5 and 6
4. Install the hydraulic valve lifters in the guides and fix them there with rubber bands.
5. Install the components in the cylinder head, making sure that the rocker arms are correctly positioned in the recesses of the guide pushers. Tighten the bolts of the rocker axles, until only by hand.
Attention! Make sure that the plungers of all pushers and valve stems are located in the center of the working surfaces of the rocker arms, and the oil holes of the rocker arms are facing the valve springs.
6. Make sure that the engine is still at the TDC position of the end of the compression stroke of the first cylinder. If necessary, correct the position of the crankshaft.
7. Tighten bolts of fastening of axes of yokes on a back directing of pushers with the demanded effort.
8. Turn the engine one revolution in the direction of normal rotation so that the pointer on the timing chain cover is again opposite the TDC mark on the crankshaft pulley. Tighten with the required effort all the remaining bolts of the rocker axles and front guide.
9. Check up serviceability of a condition and correctness of provision of a laying of a cover of a head of cylinders. At the slightest doubt, the gasket should be replaced.
10. Establish a cover on a head of cylinders, screw in screws and place sealants. Working in a spiral from the center outward, tighten the screws in several stages to the required torque. Connect the engine ventilation hoses.
11. Install the air cleaner. Start the engine and check for leaks.